Fiberoptic laser cuts reflective materials, free-form bender eliminates straights between bends
By Eric Lundin
December 3, 2012
After getting a start in the handrail business in 1990, Sharpe Fabrication Inc. relaunched itself in 1994 as Sharpe Products and started to offer general fabrication services. Two of the company’s investments, a free-form bender and a fiber-optic laser machine, reflect the company’s interest in staying abreast of technology developments.
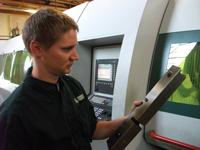
Robbie Krickeberg, laser programmer and operator at Sharpe Products Inc., shows an example of the laser machine’s capabilities.
In a competitive environment, differentiation is the key to success. The differentiator can be just about anything—specialized knowledge or accumulated experience to handle new or unusual projects; sufficient production flexibility or excess capacity to handle urgent orders; or a combination of technologies that competitors don’t have. Sharpe Products Inc., New Berlin, Wis., is an example of the last one, a company that has invested in unique technologies.
Metal fabricators have been using laser cutting machines and CNC tube and pipe benders for decades. Initially the CO2 laser was the only type available for the metals industry, but advances in various technologies have made a second type, the fiber-optic laser machine, a viable option. Likewise, bending capabilities have advanced and these days fabricators can choose from several bender types, such as roll, ram, compression, stretch, rotary, and a more recent development, the free-form machine.
Sharpe became an early adopter of fiber-optic laser technology when it purchased a machine in 2012. This, coupled with several types of bending machine, including a free-form bender that eliminates straights between bends, opens up new design possibilities for Sharpe’s customers.
A Background in Handrails
Founded in 1990 as Sharpe Fabrication Inc., the company initially fabricated a single product line: architectural railings. By 1994 the company had enough feedback from its customer base to warrant branching out, so it re-branded itself as Sharpe Products and began offering tube and pipe bending capabilities, focusing on short lead-times. It continued to round out its fleet of equipment until it had band saws, cold saws, end formers, and a variety of benders.
Despite the expansion of the services it now offers, the company never lost sight of its original niche; it still does a substantial business in handrails and handrail components, and because of this, it is accustomed to working with many alloys, both ferrous and nonferrous: carbon steel, stainless steel, aluminum, copper, and brass.
Keeping one foot in the railing market doesn’t prevent the company from making great strides into other markets. Its founder and president, Paul Krickeberg, spends a lot of time thinking about equipment purchases. His fondness for technologies shows in the company’s selection of benders, which includes roll, compression, and rotary draw, as well as its free-form bender, which uses a pivoting collet instead of bend dies. The collet pivots on two axes, providing two unusual capabilities: it allows continuously varying radii and eliminates straight lengths between the bends.
Krickeberg’s interest in new processes also is revealed in the laser machine the company acquired. He looked for a machine that would complement the company’s existing processes and bring in new business.
Laser Cuts in Reflective Materials
Figure 1Laser cutting on aluminum is a relatively new capability. The so-called reflective materials—aluminum, copper, and brass—reflect the frequency generated by CO2 lasers, but absorb the light emitted from fiber-optic lasers.
One of Sharpe’s initial criteria for a laser cutter was the machine’s diameter range. While laser cutting machines are available to cut round tube and pipe up to 20 in. OD, this would be excessive for Sharpe, whose benders top out at 6 in.
Another criteria was load and unload capability, which reflects the other critical part dimension, length.
“The parts we process usually aren’t longer than 8 ft.,” Krickeberg said.
Sharpe was interested in the ability to cut the materials often used to make decorative handrails, such as brass and copper. The company also wanted the ability to cut aluminum (see Figure 1). The requirement to cut these materials essentially eliminated CO2 lasers from the running. The mirrors in CO2 lasers usually are made from copper, which is a favored material because of its combination of reflectivity, high thermal conductivity, and high heat capacity. Brass alloys, which typically contain 65 to 85 percent copper, have similar characteristics. These alloys reflect the laser beam, so the beam can’t cut the material. However, the laser beam delivered by a fiber-optic laser is a different frequency, one that is absorbed readily by copper and copper-based alloys.
A final consideration was state of the market. Fiber-optic tube and pipe cutting lasers are relatively new to the market—Krickeberg is aware of fewer than 10 fiber-optic tube lasers in the U.S.—so it made sense to invest in a unique technology.
Ultimately, the company chose BLM’s LT (laser tube) Fiber that delivers 3,000 watts. It handles tubes from ½ in. to 6 in. OD, which nearly covers the range of diameters Sharpe’s equipment can bend (1⁄4 to 6 in.). It handles the tube lengths Sharpe processes; the loader accepts tubes up to 24 ft. and the unloader accommodates parts up to 14 ft. Likewise, it handles substantial wall thicknesses.
“We have cut parts up to ¼ in. thick. We should be able to go up to 3⁄8 in. in stainless steel, copper, aluminum, and brass,” Krickeberg said.
Fiber-optic lasers are known for cutting faster than CO2 lasers in thin material, and Krickeberg is pleased with the throughput.
“On some parts, it cuts up to 1,000 per hour,” he said.
Another big advantage for the company is the burr-free cut the laser produces. A burr is a problem for two reasons: It’s a safety hazard, and it can interfere with insertion of the tube-bending mandrel. Laser-cut parts can go straight to a bender without an intermediate deburring step.
A final consideration is how the laser machine complements Sharpe’s other processes. Because it is automated, the laser lends itself well to large lot sizes. For small-volume cutting projects, it usually makes sense to use one of the saws because they have a lower burden rate.
Exploring the Capabilities
While the company’s laser business grows, Krickeberg has been working on processing parts as efficiently as possible. It’s not exactly trial-and-error, but neither is it cut-and-dried. It takes some judgment and a knack for experimenting.
- Krickeberg has been figuring out how to get the most yield from every length of tubing.
“We’re still learning about loading long parts versus short parts,” Krickeberg said. “We’re also learning how close we can get to the end of the feedstock. There is a limit because the tube is held by a chuck.” Usually the final 3.75 in. cannot be cut by the laser because this is the length gripped by the chuck. It’s possible to remove the tube, insert the other end into the chuck, and do some cutting on the final 3.75 in., but this is rarely cost-effective. It makes more sense to design parts to accommodate a final leg 3.75 in. long.
- While most cutting processes impart some heat to the workpiece, the amount of heat a laser transfers to the material can be substantial. Reducing the heat input is important, especially when cutting aluminum and stainless steel. Three strategies are changing the assist gas mixture, changing the nozzle orifice size, and changing the order of the cutting geometry to distribute the heat more evenly.
- Krickeberg is learning to deal with a tube laser’s tendency to burn through the far wall. Usually it isn’t a problem, because the beam focuses midway through the near wall, and when the laser beam reaches the far wall, usually it has dissipated to the point that it doesn’t cut the far wall. It might put a blemish on the ID, but even this usually can be prevented by changing the settings, such as moving the focal point or reducing the power. The challenge increases as the wall thickness increases or the diameter decreases, but even so, Krickeberg has a second option.
- The vendor sells an insert that prevents spatter, and I think it would prevent burn-through also” Krickeberg said.
- Spatter is a more common problem than burn-through, but an easier one to deal with. “Spatter usually doesn’t stick to the ID too well—it usually just rubs off. We have a tool that removes spatter if necessary,” he said.
- The machine’s software estimates cutting time and material yield, which is a good benefit for quoting. In Krickeberg’s experience, the estimates are accurate; he has seen little difference between the estimates and the actual amounts.
“It’s not like bending, which has quite a number of variations,” he said. “Laser cutting is much more straightforward. You load it and you cut it.”
Responding to Customers’ Requirements
Figure 2The laser’s accuracy makes coped parts that fit snugly, making the welder’s job easier.
It’s not just a matter of learning the machine’s capabilities; Krickeberg is also exploring customers’ needs relative to the new machine.
“We’re accustomed to receiving 3-D files these days,” he said. The laser’s controller accepts files in common formats such as IGES, STEP, and PARASOLID®, so Krickeberg does not have to take any additional steps or do any programming.
Many customers still send 2-D files, and even though it sounds like a cliché, some still send in hand-drawn sketches. Krickeberg has found that preparing a file for customer approval doesn’t take much time or effort.
In addition to learning customers’ needs, Sharpe is also aware that it needs to let its customers know that it has some new capabilities, such as marking parts.
“Often an assembly has two really similar parts, or a part that is nearly symmetric, so we can mark the parts to make the assembler’s job much easier. It’s a simple matter of pressing a button. One is labeled ‘Marking’ and the other is labeled ‘Cutting,’” he said.
Common applications for fabricated items include copes, slots, holes, and notches (see Figure 2). Also, because the company started in the handrail business, the laser is ideally suited to this niche, because it can cut decorative, ornamental patterns.
“Engineers probably aren’t designing aluminum tube with holes for laser cutting,” he said. It’s similar to getting the word out about the company’s free-form bender. “The varying radius and continuous bends lend themselves to interesting designs,” he said.
This isn’t to imply that the company is focused solely on laser cutting followed by bending.
“So far we have used the laser on parts that require bends—our existing business,” Krickeberg said. “Right now we’re going after laser-cut-only parts, which would be a new business segment for Sharpe.”